Metal Roofing – An Attractive, Durable Option For Residential Homes and Commercial Structures
Metal Roofing is an attractive, durable option for residential and commercial buildings. It can reduce cooling costs, improve energy efficiency, and help protect the building’s structure and interior from water damage.
Start by removing old shingles and cleaning the roof surface. Then, install a protective underlayment and begin adding panels. Work from the eaves, working toward the ridge and ensuring each panel overlaps the previous one. Contact Helena Metal Roofing Company now!
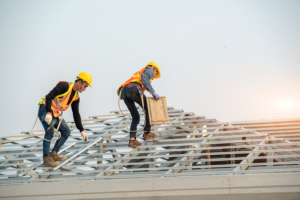
Many homeowners choose metal roofing for its durability, long lifespan, and energy-saving properties. It also adds a beautiful design to your home and can be customized with color and finish options. It can withstand nearly any type of weather condition without compromising the integrity of your home or business.
Unlike asphalt shingles, which are prone to cracking and leaking in bad weather, metal roofs last years without any signs of damage or wear. They have a high resistance to hail and other debris as well. The fact that they can withstand such extreme weather conditions makes them a great option for areas that are often hit by tropical storms and hurricanes.
When it comes to metal roofs, the best advantage is that they are easy and affordable to maintain throughout their lifespan. They do not rust, leak or mold and can be easily repaired with little to no maintenance effort. Rain and snow slide off them quite efficiently, which greatly reduces the chances of water damage to your ceilings, walls or interior furniture.
Because they reflect sunlight instead of absorbing it, a metal roof can save you on your energy costs in the summer by keeping your house cool. This is especially helpful if you live in a hot area and need to keep your electricity bill low.
Another energy savings benefit of metal roofs is that they are very effective in insulating homes or buildings in cold climates. They help keep the heat inside during the winter and prevent the cold air from escaping, which saves on heating expenses.
Finally, when you are shopping around for a roofer to install your metal roofing, make sure you get prices for both materials and labor. This will allow you to compare apples to apples when getting bids.
When choosing the metal for your roof, beware of “barn tin” or other types that have visible fasteners. If the fasteners leak, it will be readily apparent in a shed, but in a home, it can soak through insulation, framing and drywall before anyone notices.
Installation
A metal roof is a long-lasting, durable option for residential homes. It can withstand high winds and heavy snow loads, and is energy-efficient, reflecting sunlight to keep the home cooler. While the initial cost is higher than traditional shingles, metal roofing pays off in longevity and energy savings.
A qualified metal roofing contractor will walk you through your options and help you choose the best metal to suit your climate, needs, and budget. The most common metals are aluminum, steel, and galvalume. The differences between these choices include weight, strength, corrosion resistance, and color. Aluminum is lightweight and resistant to corrosion, making it a good choice for coastal regions with salty air. Steel is stronger and resists rust. However, it is much more expensive than aluminum.
Before beginning any installation work, your roof should be inspected for signs of deterioration and structural damage. This step is vital to ensuring the integrity of your roof, and also ensures that your installation follows local building codes and regulations.
The first steps in installing a metal roof are to install drip edges along the eaves and remove any existing shingles or underlayment. Then, the roof should be swept clean and prepared for the new underlayment and panels.
Underlayment is an important part of the installation process because it protects against moisture infiltration and provides a smooth surface for the panels. It is typically adhesive-backed and is unrolled across the roof, overlapping the previous layer by six to eight inches. A tin sealant can be applied to the underlayment for added protection.
Next, the metal panels are installed and interlocked or overlapped. During this phase, care should be taken to ensure that all fasteners are tight and secure, but not overtightened. Over-tightening can cause the panel to warp or pull away from the roof. Using pancake head fasteners helps prevent this from happening.
Finally, flashing and trim are installed to prevent water leaks at the seams and intersections of the roof. A good installer will inspect all flashing and trim for proper installation.
Maintenance
A well-installed metal roof is fairly low-maintenance, but regular cleaning and inspections are vital to extend the life of a metal roofing system. In addition, regular maintenance can save money by preventing more expensive repair or premature replacement costs.
Structural maintenance includes cleaning, visual inspections, and addressing any potential problems promptly to avoid leaks. In addition, the gutters and drains should be cleaned out about twice a year to prevent clogging. The leaves, sticks, and other debris that build up in these areas can cause water to back up onto the roof or your home, potentially causing corrosion and stains. A professional can help you choose and install the right gutter guards to prevent this from happening in the future.
Most newer metal roofs are not susceptible to leaking, but it’s important to inspect the entire structure. In particular, look for separating or loose panel seams, flashing that has cracked, rusty spots or is corroded, and other signs of damage. If you notice any leaking, it’s a good idea to contact a metal roofing professional for fast repairs to minimize the risk of water infiltration and other damage.
Both standing seam and screw-down metal roofs require regular maintenance. However, since screw-down metal roofs have exposed fasteners, they may need to be checked more frequently than standing seam metal roofs. It’s important to check that the fasteners are secure and haven’t backed out. This can happen for a variety of reasons, including wind uplift and the natural expansion and contraction of the panels over time. The fasteners should also be checked for corroded washers, as this can lead to leaks in the future.
Other structural maintenance includes checking the integrity of the flashing around penetrations such as chimneys, vents, and skylights. This is a common source of metal roof leaks, and it’s essential to make sure the flashing is properly sealed. A professional will look for areas where the flashing has cracks, rusty spots, or is missing altogether. These can be repaired with caulking and will prevent water from entering the home. Additionally, a professional can recommend roof sealants to ensure the waterproof properties of your metal roof are intact.
Warranty
A metal roof is a significant investment, and the warranty offered by the manufacturer and supplier is a great way to provide confidence that the product will stand up to the elements. However, homeowners should take the time to read through the warranty fine print and understand what is covered and what is not.
Manufacturer warranties typically cover the integrity of the metal roofing materials. They will include details such as the length of coverage and a list of exclusions and requirements that must be met in order to keep the warranty active. For example, the manufacturer may require that all metal roofs be regularly inspected and maintained by a licensed contractor in order to avoid voiding the warranty.
Workmanship warranties, on the other hand, cover the work that a licensed contractor does in installing the metal roofing system. They will include details such as the clips and fasteners used in a standing seam project, or how the trim is installed on a corrugated metal roof.
It is important to note that metal roofing warranties do not cover problems due to age or normal wear and tear, such as cracking, splitting, fade or granule loss. This is something that many consumers miss when reading through the warranty, and it can lead to costly repairs and replacements.
The warranty will also specify whether the metal roofing is prorated or non-prorated, and if it can be transferred to subsequent owners. This is important, as a prorated warranty will diminish the value of the metal roofing over time, while a non-prorated warranty will remain in effect for its entire lifespan.
Finally, it is important to remember that the quality of a metal roof is not only dependent on the metal itself, but also on the substrate and coating used. The higher quality products, such as Galvalume steel and Kynar 500 (PVDF), will generally come with better warranties than those with lower grade substrates and coatings.
By taking the time to understand these nuances of a metal roof warranty, homeowners can rest assured that their metal roofing will stand up to the elements and protect their home for years to come. The peace of mind that comes with a quality product backed by robust warranties is well worth the added expense.